Forming Sheet Metal Parts with 3D Printing
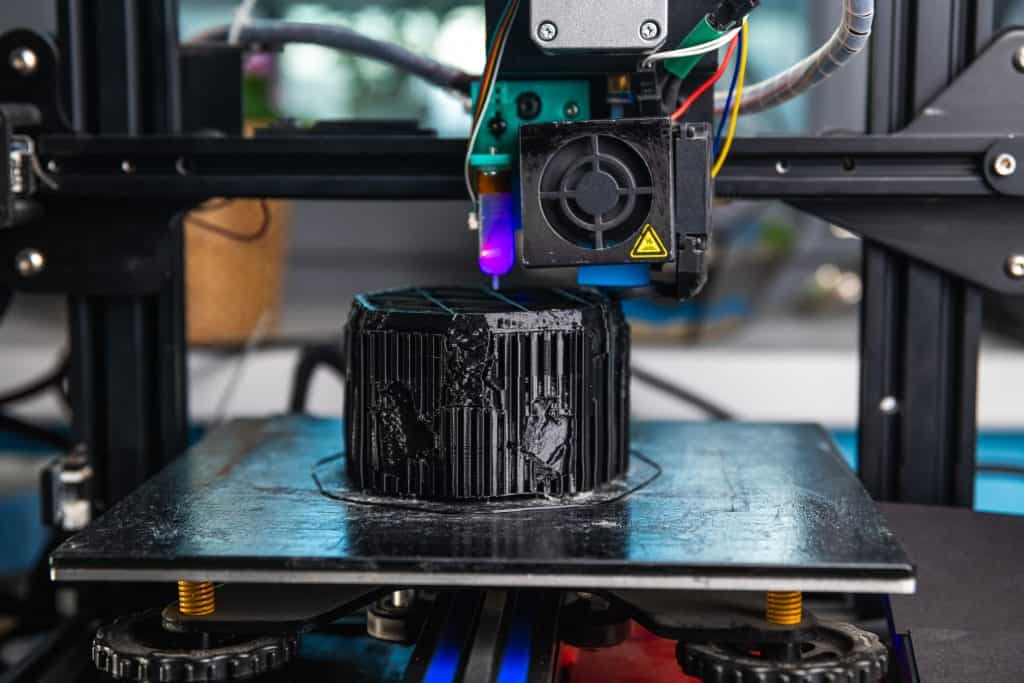
Traditional sheet metal forming methods have challenges, such as high costs and long lead times for tooling. These issues slow down the production process, especially when dealing with complex geometries.
One solution is to use 3D printing to create custom dies and tools. This approach allows you to rapidly produce specialized tools that meet the precise requirements of each project, reducing both time and costs.
Read on to learn more about how integrating 3D printing with sheet metal forming enhances design, customization, and prototyping.
How 3D Printing Can be Used in Sheet Metal Forming
Integrating 3D printing with sheet metal forming opens many doors for your product development, by paving the way for greater precision and creativity. Let’s explore how this integration transforms the process:
- Custom Tooling and Fixturing: Creating tools for sheet metal forming, such as dies for stamping or bending, is expensive and time-consuming. With 3D printing, you can precisely produce these parts to your specifications, cutting costs and wait periods. You can make quick adjustments and iterations as needed, since the process is agile and adaptable to design changes.
- Complex Geometry: With sheet metal forming alone, it’s a struggle to create intricate indentations, curves, and complex shapes. But, when combined with 3D printing, no element is too fine to capture or reproduce as 3D printers can lay down material according to almost any complex pattern. Leverage a 3D printing tool to achieve the precise details you want to use in forming the sheet metal.
- Rapid Prototyping: Manufacturers must test and refine designs before production. With 3D printing, you can quickly produce prototypes of sheet metal parts to evaluate their fit, form, and function. This means potential issues are identified and resolved early, ensuring the final product meets all design and performance expectations without costly surprises down the line.
What Are the Benefits of Forming Sheet Metal Parts with 3D Printing?
Integrating sheet metal forming and 3D printing unlocks several advantages that empower designers and engineers to push boundaries. Let’s take a look at the top benefits to understand how this pairing can reshape manufacturing:
- Design Flexibility: By combining 3D printing and sheet metal forming, you can open up new opportunities for innovative designs and create parts with intricate details, complex profiles, and unique aesthetics.
- Tooling and Fixturing: 3D printed tooling and fixtures can be quickly modified as needs change during product development and production. Amendments to the part design are simple to incorporate by updating the digital files and reprinting tooling components.
- Rapid Prototyping: One primary way 3D printing complements sheet metal forming is by allowing fast and easy prototyping. Before committing to production hardware, you can test design concepts, sizes, and shapes using 3D-printed tooling. This gives you valuable early feedback that you can use to refine specifications without significant delays or expenses.
Expand Your Manufacturing Business’s Digital Presence With MFG
Benefits include:
- Increased visibility to potential clients with a tailored company profile
- Connect with serious prospects actively looking for your products or services
- View and respond to RFQs from vetted purchasers
- Cultivate long-term business partnerships
- Enjoy significant savings on material costs compared to major e-commerce sites
Sign up for MFG to find new sheet metal projects and customers and start growing your customer base today!