3D Printing vs Plastic Injection Molding
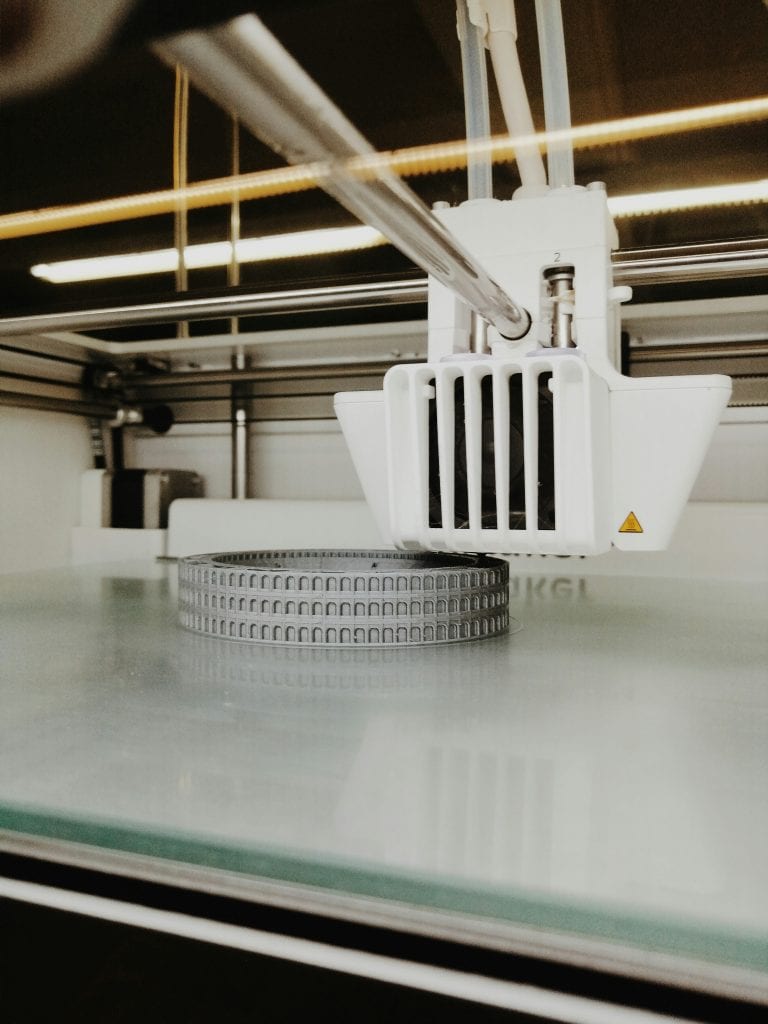
Understanding the differences between 3D printing and plastic injection molding is crucial for producing high-quality custom parts efficiently. While both technologies are used for efficient part production, they are not interchangeable.
3D printing and plastic injection molding differ in approach, design, cost, speed, and more. Understanding these factors is critical for making an informed decision about which method to use for your project.
Read on to learn more about what distinguishes 3D printing from plastic injection molding and discover which method is right for your custom manufacturing needs.
What Is 3D Printing?
3D printing, also known as additive manufacturing, is an innovative process that constructs parts layer by layer from a digital blueprint. The journey begins with a 3D model created using Computer-Aided Design (CAD) software. This model is then digitally sliced into ultra-thin horizontal layers, creating a roadmap for the 3D printer.
The printer follows this roadmap, depositing material — typically plastic or resin — one layer at a time. Each layer is fused to the previous one using heat, light, or lasers, gradually building up the complete object. This additive approach allows for the creation of complex geometries that might be challenging or impossible with traditional manufacturing methods.
Several 3D printing technologies exist, each with unique capabilities:
- Fused Deposition Modeling (FDM)
- Selective Laser Sintering (SLS)
- Stereolithography (SLA)
These methods differ in how they soften, apply, and fuse materials, offering varying levels of precision, speed, and material compatibility. 3D printing excels in producing intricate parts and enables rapid prototyping, making it a valuable tool for industries ranging from aerospace to healthcare. Its ability to quickly turn digital designs into physical objects has revolutionized the product development process, allowing for faster iterations and more efficient customization.
What Is Plastic Injection Molding?
Plastic injection molding is a sophisticated manufacturing technique that produces plastic parts by injecting molten plastic into a custom-designed mold. The process begins, like 3D printing, with a CAD-created 3D model. However, this model serves as the basis for designing the mold itself, rather than directly guiding part creation.
The mold design is crucial, incorporating three key elements:
- The core
- The cavity
- Cooling channels
Once designed, the mold is precision-machined, typically from steel or aluminum.
The production process follows these steps:
- Plastic pellets are heated to their melting point.
- The resulting liquid plastic is injected into the mold under high pressure.
- This pressure ensures the plastic fills every detail of the mold cavity.
- The plastic cools and solidifies within the mold.
- Once fully cooled, the mold opens and ejects the finished part.
Plastic injection molding is particularly effective in mass production scenarios. Its hallmarks are speed and consistency, allowing for the rapid, repeatable production of identical parts. This makes it an ideal choice for large-scale manufacturing where uniformity and efficiency are paramount.
The technique’s ability to produce high volumes of consistent, high-quality parts has made it a cornerstone of modern manufacturing across various industries, from automotive to consumer goods.
3D Printing vs Plastic Injection Molding
The fundamental distinction between 3D printing and plastic injection molding lies in their core processes. 3D printing, an additive manufacturing technique, builds objects by stacking layers of material. In contrast, plastic injection molding fills a pre-made mold with molten plastic, forming the part in a single step.
Plastic injection molding requires an additional step: designing and machining the mold. This upfront work can extend the initial timeline. However, once the mold is ready, production can proceed rapidly. 3D printing, while quicker to set up, may require more time per part produced.
Surface quality is another key differentiator. Injection molded parts often boast smoother surfaces straight out of the mold. 3D printed items, on the other hand, may exhibit visible layer lines, potentially calling for post-processing for a refined finish.
Aside from their overall processes, 3D printing, and plastic injection molding have several other key differences:
-
Approach To Design
3D printing offers unparalleled design flexibility, enabling the creation of complex geometries and rapid iterations without molds. This makes it ideal for prototyping and low-volume, custom production. Plastic injection molding, while less flexible, excels in high-volume production of parts with consistent dimensions. The initial mold investment pays off in unmatched repeatability and cost-efficiency at scale.
-
Manufacturing Materials
3D printing supports a wide array of materials, including various plastics, resins, metals, ceramics, and composites. This versatility allows for the production of commercial-grade parts across diverse applications. Plastic injection molding, though somewhat more limited, remains highly adaptable. It typically uses commodity plastics like ABS, PP, and PE, as well as engineering-grade plastics such as PA, PC, and PEEK.
-
Cost-Effectiveness
The cost structures of these methods differ significantly. 3D printing boasts lower initial costs due to the absence of mold expenses, making it cost-effective for small runs and prototypes. However, per-unit costs remain high for large volumes. Conversely, plastic injection molding requires substantial upfront investment but offers remarkably low per-part costs in mass production, making it the go-to choice for high-volume manufacturing.
-
Speed
Production speed varies between these methods. 3D printing offers quick turnaround from design to finished part, ideal for rapid prototyping. Plastic injection molding has longer setup times due to mold creation but achieves extremely fast production rates once operational. While individual 3D-printed parts may take longer to produce, injection molding’s efficiency in mass production is unmatched.
-
Quality
Both methods can yield high-quality, precise parts suitable for various applications. Injection molding typically produces parts with superior surface finish, durability, and dimensional consistency, though care must be taken to prevent issues like splay. 3D printing quality depends on the specific technology used, layer thickness, and post-processing techniques applied. Each method has its strengths, and the choice often depends on specific project requirements and quality standards.
Make An Informed Choice
Selecting between 3D printing vs plastic injection molding hinges on your specific project requirements and business objectives. Each method offers distinct advantages that cater to different manufacturing scenarios.
3D printing shines in situations that demand:
- High design flexibility
- Rapid prototyping
- Low-volume production
- Customization
- Complex geometries
Plastic injection molding excels when you need:
- High-volume production
- Consistent part quality
- Cost-effective large-scale manufacturing
- Durability and superior surface finish
To make the right choice, carefully evaluate your project’s key factors:
- Design complexity
- Production volume
- Budget constraints
- Quality standards
- Time-to-market requirements
Consider both short-term needs and long-term manufacturing goals. For instance, you might use 3D printing for prototyping and initial low-volume runs, then transition to injection molding as demand increases.
Remember, these methods aren’t mutually exclusive. Many successful manufacturing strategies incorporate both techniques at different stages of product development and production.
For expert guidance in choosing between 3D printing vs plastic injection molding and optimizing your manufacturing process, consider partnering with MFG. Our platform connects you with a network of manufacturing professionals who can help tailor a solution to your specific needs, ensuring you leverage the right technology for your project’s success. See how MFG can help you with your manufacturing needs.