Guide to Plastic Injection Molding
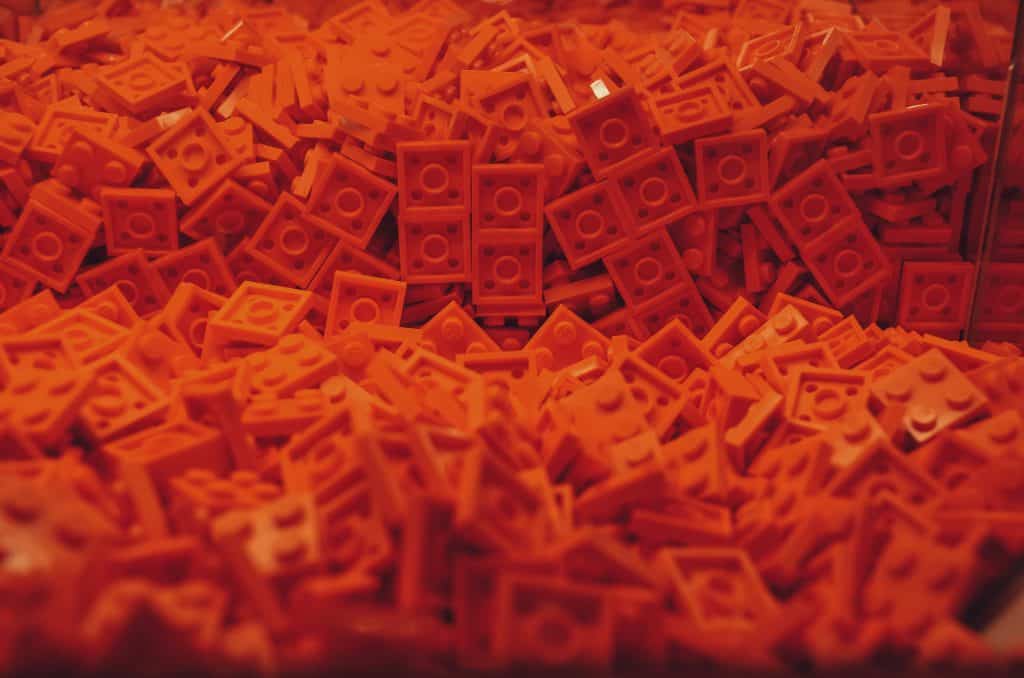
From Lego bricks to sophisticated car parts and medical devices, plastic injection molding is a leading technology for creating plastic components. While it’s a popular choice, it’s not the only manufacturing method available. Alternatives like 3D printing, thermoforming, rotational molding, and extrusion offer different benefits for various production needs.
With so many options at your disposal, how do you determine if plastic injection molding is the right fit for your manufacturing requirements? This guide will walk you through the process, highlighting its key advantages and important considerations. We’ll break down the steps involved, helping you make an informed decision about whether plastic injection molding aligns with your production goals.
What Is Plastic Injection Molding?
Plastic injection molding is a manufacturing process in which melted plastic is injected into a mold under high pressure. This liquid plastic is then allowed to cool and solidify to form the desired shape. The process is incredibly flexible and is used to create small, intricate parts for precise engineering applications and larger components for more utilitarian uses such as trash cans or car bumpers. Its speed and consistency make it ideal for the mass production of plastic parts.
3D printing vs. plastic injection molding
It’s important to clearly differentiate 3D printing vs. plastic injection molding. 3D printing is an additive manufacturing process in which softened plastic (typically from a filament) is pushed through a nozzle by rollers and added in layers, one stacked upon the other, until the full shape of the part is complete.
By contrast, plastic injection molding relies on liquifying plastic pellets, not a filament. These pellets are melted down and then injected into a pre-fabricated steel or aluminum mold. Once cool and solid, the part is then ejected. Since the plastic is not laid down in stacks but instead fills the mold all at once, horizontal lines are not a common surface defect in plastic injection molding.
How Injection Molding Is Commonly Used In Manufacturing
Plastic injection molding has come a long way since its inception in 1872, when John Wesley Hyatt and his brother Isaiah pioneered the technology. Initially aiming to create better billiard balls from plastic rather than ivory, their innovation laid the groundwork for the diverse applications we see today.
In modern manufacturing, injection molding has become a cornerstone technique across numerous industries:
- Automotive: Produces various components, from interior trim to under-hood parts
- Consumer Electronics: Creates device housings and intricate internal components
- Medical: Fabricates precise instruments, syringes, and even implantable devices
- Toys: Shapes durable, colorful playthings for children of all ages
- Packaging: Forms containers and lids for a wide range of products
The versatility of injection molding allows it to meet the demanding specifications of these diverse sectors. For instance, in the medical field, the process ensures the production of sterile, high-precision parts crucial for patient safety. In the consumer electronics industry, it enables the creation of sleek, durable casings that protect sensitive internal components. This manufacturing method’s ability to produce consistent, high-quality parts at scale has made it indispensable in today’s industrial landscape. From the smallest electronic components to large automotive parts, plastic injection molding continues to shape the products we use daily.
Advantages of Plastic Injection Molding
Plastic injection molding offers distinct benefits that set it apart from other production methods:
-
Cost-Effective Mass Production:
While initial setup costs can be high, injection molding becomes increasingly cost-efficient as production volumes rise. The per-unit cost decreases significantly with larger runs, making it an economical choice for high-volume manufacturing.
-
Exceptional Efficiency:
This process is notable for its minimal waste and rapid production rates. Once molds are finalized, parts can be produced in seconds, leading to impressive output volumes. The speed and efficiency of injection molding contribute to its popularity in industries requiring large quantities of identical parts.
-
Material Versatility:
Injection molding accommodates a wide spectrum of plastics and elastomers. This flexibility allows manufacturers to select materials that best suit their specific project requirements, whether it’s durability, heat resistance, or flexibility. The ability to work with various materials contributes to the method’s widespread adoption across numerous industries.
-
Precision in Complex Designs:
A key advantage of injection molding is its capacity to create intricate and complex shapes with high accuracy. This precision ensures consistent quality across production runs, meeting the exacting standards of industries that demand tight tolerances and dependable performance.
5 Steps of the Plastic Mold Injection Process
To create high-quality parts with consistency and efficiency, manufacturers must follow the following injection molding steps, from mold design to cooling and ejection.
- Step 1: Mold Design and Creation
This initial step is critical as it shapes the entire plastic injection molding process. Using CAD software, designers create a mold design that defines the part’s features and quality. The mold is typically made from durable materials like steel or aluminum to withstand high heat and pressure. It includes essential elements such as cooling channels, ejection mechanisms, and mold flow supports to guarantee optimal results.
- Step 2: Material Selection
Choosing the right plastic is fundamental for determining the part’s performance, appearance, and cost-effectiveness. Engineers consider various factors, including mechanical and thermal properties, chemical resistance, and aesthetics. Common materials include ABS, Polycarbonate, Polystyrene, Polypropylene, and Polyethylene, each offering unique characteristics suited to different applications.
- Step 3: Injection Molding Machine Operation
Once the mold is ready and material selected, the machine comes into play. Plastic pellets are heated to their melting point in a hopper. The molten plastic is then injected into the mold cavity at high pressure, typically between 10,000 to 30,000 psi. Precise control of speed, pressure, and temperature is crucial to ensure part quality, and to avoid defects like sink marks, voids, or weld lines.
- Step 4: Cooling and Solidification
After the plastic is injected into the mold, it needs to cool and solidify. This process is hastened by cooling channels embedded into the mold that circulate a coolant (typically water or a glycol-water mixture). The design of these cooling channels can prevent part warpage or internal stress. Cooling time will depend on the part’s thickness and the efficiency of the cooling system.
-
Step 5: Ejection
With the part cooled and solidified, it’s time for the final step of the plastic injection molding process. An ejection system, often using strategically placed pins or plates, pushes the part out of the mold cavity. Careful design of this system is necessary to ensure the part is removed without damage or visible marks, maintaining its integrity and appearance.
Design Considerations for Injection Molding
The best parts are designed with their manufacturing process in mind from the very beginning. Buyers should seek manufacturers that prioritize design for manufacturability (DFM) principles. DFM involves collaboration between designers and manufacturers to optimize the design, minimize unnecessary complexity, reduce the number of components, and enhance the ease of assembly. This helps avoid potential production issues down the road.
Additional design considerations for injection molding include:
- Wall Thickness: Maintaining consistent wall thickness is key for preventing defects. Generally, wall thickness should range between 1.5mm and 4mm, depending on the material chosen. This ensures uniform cooling and reduces the risk of warping or sink marks. While 3D printing can achieve thinner walls (around 0.6mm) due to its laser curing process, injection molding requires slightly thicker walls for optimal results.
- Draft Angles: Incorporating draft angles (typically 1 to 2 degrees) on part walls permits easier ejection from the mold. This small taper significantly reduces the risk of damage to both the part and the mold during the ejection process, ensuring smoother production and higher part quality.
- Undercuts: While undercuts can add functional or aesthetic value, they complicate mold design and part ejection. Designers should carefully evaluate the necessity of undercuts and explore alternative solutions where possible to simplify the molding process and reduce production costs.
- Surface Quality: Factors such as gate design, venting, and material selection play important roles in determining the final surface quality of the part. By refining these elements, manufacturers can minimize common defects like splay, flash, and air traps, resulting in higher-quality finished products.
Choose MFG to Source the Best Custom Manufacturer For Your Product
Plastic injection molding has proven itself as a cornerstone of modern manufacturing, offering an efficient, versatile, and cost-effective method for producing plastic parts. Its streamlined 5-step process enables rapid, consistent production, making it ideal for high-volume custom manufacturing needs.
If you’re in search of a custom manufacturer for your product, MFG offers a comprehensive solution. Our innovative online marketplace serves as a hub connecting a vast network of 26,000 manufacturers with 75,000 buyers, streamlining the supplier discovery process.
MFG’s platform provides:
- Simplified Supplier Discovery:
Our interactive marketplace facilitates easy connections between manufacturers and buyers, simplifying your search for the perfect production partner.
- Enhanced Collaboration:
With global manufacturer listings and direct order management, you can efficiently collaborate with potential suppliers. On average, buyers receive four quotes from US manufacturers alone, giving you a range of options to consider.
- Advanced Features:
MFG offers a suite of tools to optimize your manufacturing journey:
- Detailed search functionality
- Quick and easy RFQ posting
- Peer reviews for informed decision-making
- SEO-friendly profiles to boost visibility
- Intelligent RFQ routing to match you with suitable manufacturers
By leveraging MFG’s platform, you can streamline your search for the ideal custom manufacturer, saving time and resources while ensuring you find a partner that meets your specific production needs.
Explore how MFG can help you locate the right custom manufacturer for your project, click the link below to learn more about our services and start your journey towards optimized production.