How To Fix Splay In Injection Molding
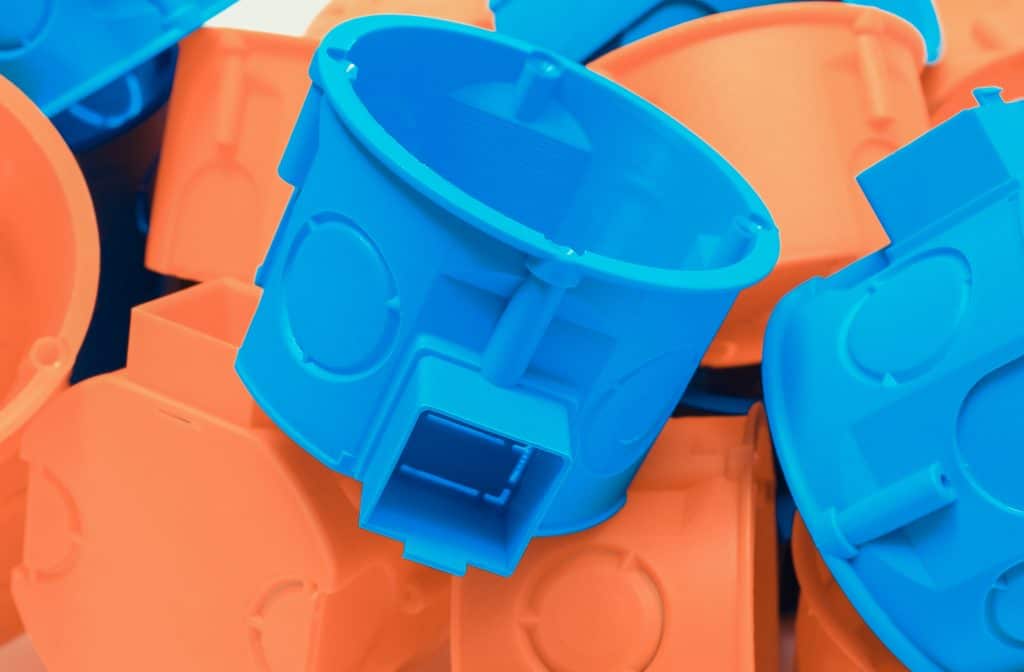
Splay is a cosmetic defect that can sometimes occur in parts created with injection molding. It can be a frustrating problem, compromising the quality and appearance of your part or final product. When significant, splay can lead to dimensional inaccuracies and mechanical issues, reducing the value and usability of new pieces. Understanding and addressing this issue is important for maintaining high production standards and keeping waste to a minimum.
In this article, we break down what causes splay and explain the practical solutions to fix it so that your parts can always meet the highest quality standards.
What is Splay?
Splay, also known as silver streaks or splash marks, is a surface marking on injection molded objects characterized by lines or patterns on the part’s surface. These marks can appear as silvery, cloudy, or streaky areas, detracting from the aesthetic quality and potentially impacting the part’s functionality. Splay is often a sign of issues within the molding process and can mean parts fail to meet quality requirements. This can result in some parts requiring rework or rejection, increasing production costs and time.
How Do Splay Injection Molding Flaws Happen?
Splay in injection molding typically occurs due to factors like excessive moisture, improper drying, overheating, or shearing stress during the injection molding process.
In this manufacturing approach, a material is melted and poured into a mold. The mold is then allowed to cool, and the material solidifies. Once solid, the part is removed from the mold. This is in contrast to 3D printing, in which parts are manufactured by layering fine sheets of material on top of each other.
Let’s take a closer look at how the injection molding process can go wrong and cause splay:
Too Much Moisture
- The use of too much lubricant or grease within a mold can result in splay. Lubricants are regularly used to encourage the flow of material and reduce friction during molding. When the plastic or resin is heated as part of the injection molding process, water in the lubricant can turn to steam. This trapped vapor can produce streaks and bubbles on the part’s surface, which are examples of splay. If your part comes out of the mold and already has splay marks, this is the first problem to consider.
Poor Ventilation
- Poor ventilation can also cause splay by trapping air within the mold cavity. This trapped air is then compressed and mixed with the plastic, leading to splay marks on the surface.
Improper Drying
- Incorrect drying can also lead to splay. In plastic injection molding, the material must be dried for exactly the right amount of time at exactly the right temperature. If either of those metrics are off, splay can occur. Drying times that are too short don’t give the material enough time to bond uniformly, resulting in visible defects.
Excessive Heat
- Excess heat is another common cause of splay. Incorrect temperature settings can lead to unequal melting or burning of the material. Look for burn marks or areas that are sticky to identify whether excessive heat is the source of your splay problem.
Shearing
- Shearing is the fourth potential cause. Shearing refers to excessive mechanical stress applied to molten plastic as it is forced through the injection nozzle and into the mold cavity. High shear stress can occur due to several factors, including high injection speeds, narrow gates, or improper mold design. When the material experiences excessive shearing, it can degrade the polymer chains, leading to material separation and resulting in splay. If you suspect shear stress is the cause of your splay, be sure to check your speeds, gate dimensions, and mold design.
How to Fix Splay Injection Molding Issues
Addressing splay in injection molding requires a methodical approach to troubleshooting and problem-solving. By following a series of targeted steps, manufacturers can effectively identify and eliminate the root causes of splay, ensuring high-quality, defect-free parts. Here’s a comprehensive strategy for tackling splay:
Identify The Root Cause
- If you’re wondering how to get rid of splay injection molding defects, the first step is to identify the root cause. Begin with a thorough visual inspection of the affected parts, noting the exact location and appearance of the splay marks. Look for patterns or consistencies across multiple parts to narrow down potential causes.
- Document your findings and use this information to guide your troubleshooting efforts. If possible, make controlled changes to your process parameters one at a time, observing the impact on splay formation. This systematic approach will help you isolate the primary cause and develop an effective solution.
Check The Materials
- Ensure that your resin pellets are completely dry before going into the injection molding process. Any kind of moisture can be problematic for your finished part. Use a desiccant dryer or other appropriate drying equipment to ensure that resins are entirely moisture-free.
Optimize Temperatures
- Too high or too low melt temperatures can contribute to splay. Adjust the barrel, nozzle, and mold temperatures to ensure the plastic melts and flows consistently. Proper temperature settings help prevent material degradation and improve flow, reducing the risk of splay.
Adjust Injection Speed
- High injection speeds can lead to turbulent flow and air entrapment in the molten plastic, resulting in splay. Lowering the injection speed can help reduce turbulence and prevent surface defects like splay.
Maintain Your Mold
- Sometimes, the problem is with the mold, not the material. Regularly inspect and maintain the injection mold to ensure proper operation. This includes cleaning molds out regularly to ensure proper venting and remove contaminants.
Consult Experts
- If you continue to have splay issues despite your troubleshooting efforts, consider consulting with injection molding experts or material suppliers, like MFG, for additional guidance and support.
Where To Order High-Quality, Splay-Free Parts
Splay can be a frustrating problem when working with plastic injection molded parts, causing unsightly surface imperfections and impacting the functionality of your parts. However, it’s often easy to reverse with a few simple reconfigurations. If you’re looking for a manufacturer that understands how to create splay-free parts at affordable prices and efficient speeds, MFG can help.